5S Lean
An Introduction to Lean 5S
It’s no secret that maintaining an efficient working environment is great for providing one with peace of mind. But waste doesn’t usually manifest on purpose. The “I’ll just take care of that later” mindset can take hold of us all, especially when we’re in the midst of an important task. However, practicing constant vigilance in waste reduction – even when you think you “don’t have time” for it – will actually save time in the long run by mitigating future waste.
The 5S methodology improves workflow and cuts down on several types of waste, making it an effective Lean tool that can improve the outcomes of design and construction projects.
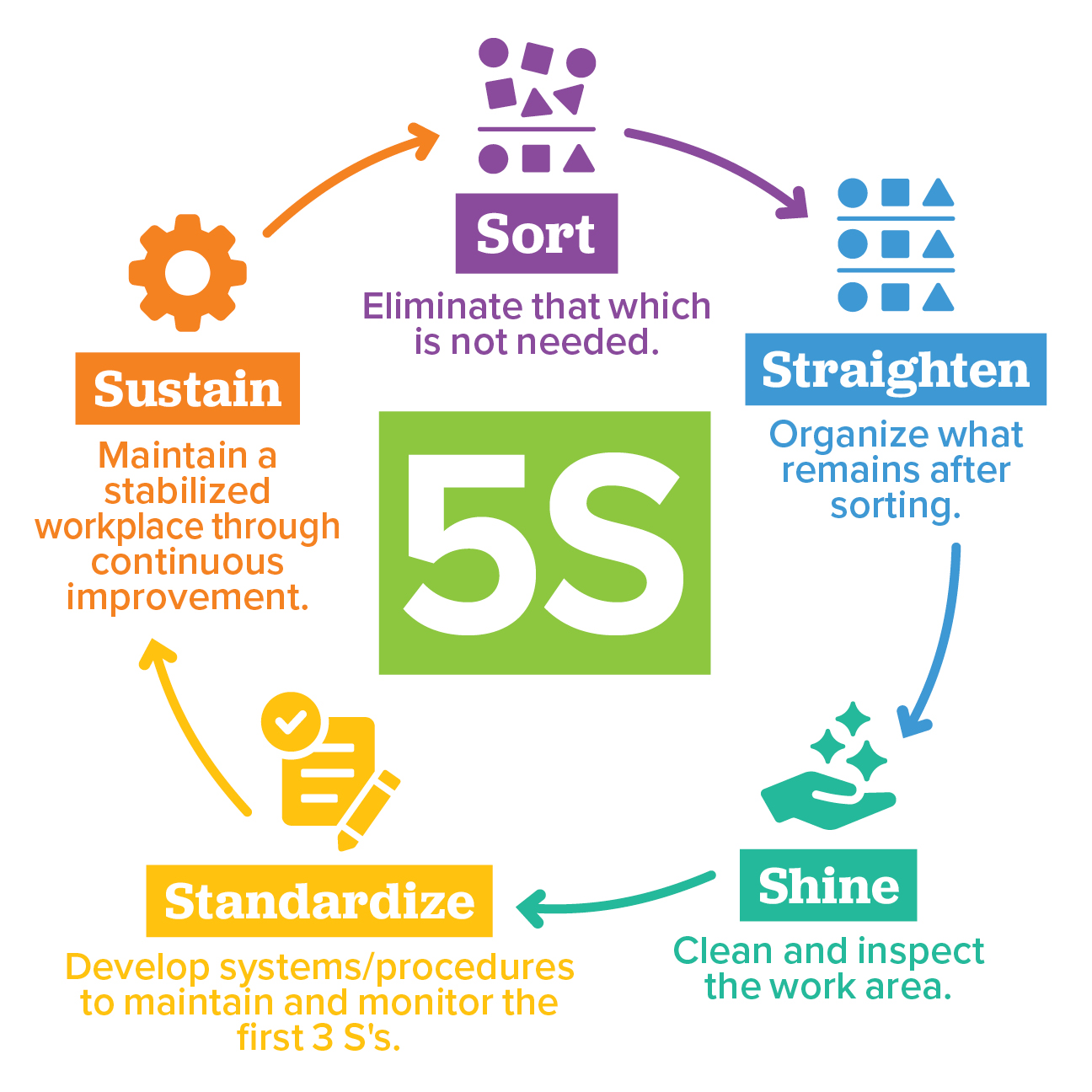
What is 5S?
A disciplined approach to maintaining order in the workplace and using visual controls to eliminate waste. The 5S words are Sort, Set in Order, Shine/Sweep, Standardize and Self-Discipline/Sustain.
The 5s System: A Mindset
The 5S mindset encourages workers to only have materials, information, and equipment where it is needed and when it is needed. It is crucial to plan your work and understand the process and handoffs, which allows workers to focus on the materials and tools needed to create maximum flow efficiency.
The goal of a 5S system is to keep work and organization simple. Simple is not always easy, so the 5S process helps to provide a lens through which to analyze the state of organization and workflow in the workplace.
The 5S Methodology
5S for workplace organization is a five-step structure for improving productivity, efficiency, quality and enhancing safety in the workplace. The 5S steps are…
1. Sort
Sort through materials, tools, and information to identify what is necessary, what is sometimes needed, and what is not needed at all. In an ideal state, anything that is not needed in that place and in that moment is waste. Clutter creates hazards in the workspace which can lead to worker injuries, while clutter in a file structure and information can lead to misinformation, defects, and uninformed decisions. In a cluttered work environment, people waste time searching for things when that time could be used to deliver value.
2. Set in Order/Straighten
Create a place for everything and keep it there until it is needed. Identify how, when, and why materials, tools, and information will be used and accessed. This allows for the set-in-order mechanism to be aligned with the process or flow of work. For example, would it eliminate waste to have a trash can under each cut station? This is the stage for considering these ideas.
3. Shine
Continuously improve and optimize your workspace. When everything has a place and it is clear where everything goes, that is a visual cue that makes it easy to recognize when something is out of place. Shine can consist of visual cues of where materials go, or it can take the form of file-naming structures to easily see where the latest file is. Afterwards, take the time to understand why your process may not be working and improve it.
4. Standardize
Once you have “Shined,” standardize your system for workplace cleanliness, data and information organization, and project file structures. Repeated and standardized processes are needed not only to allow for continuous improvement to occur, but also to keep work efficient. Workers know what to expect when work is standardized and less time can be spent overexplaining simple processes.
Once you standardize a process, you can also add it to your onboarding process for future team members.
5. Self-Discipline/Sustain
Sustain processes that work and have the self-discipline to not allow processes to get bogged down by waste. Make the working conditions and processes consistent so it’s easy to see when something is out of place or when the standard is not being met.
5S in Lean
5S supports Lean design and construction methodologies in several ways. At its core, 5S is about respect for people, ensuring that the people have the tools and resources needed to do their work efficiently. Utilizing 5S methodologies also allows teams to remove waste from the workspace and make workflows more efficient.
How 5S Makes Us Better
5S provides numerous benefits for field workers, project teams, and organizations alike. Everyone likes an organized work space with clear information flows, but few grasp the degree to which practicing 5S can improve projects and their outcomes. The impact of 5S can chiefly be seen in four different areas.
Safety
Increased focus on organization on the jobsite leads to enhanced safety, reducing some of the common project safety hazards such as slips, trips, lifting or stress-related injuries. With fewer materials strewn about the workspace, workers are at less of a risk of tripping over something unexpected or having a material crash down on them. Making processes safer is a key component to the Lean mindset.
Quality
5S helps increase quality in the field by reducing mix-ups of materials and the utilization of damaged materials. Additionally, defective or broken tools are tagged and not used (which enhances safety as well!)
An uncluttered workspace also allows people to have more mental and physical room to focus on the work itself, which leads to more quality outcomes for the customer or stakeholder.
Productivity
Workers are more productive when their workspace is well-organized, allowing them to quickly access materials and information. When employees spend less time searching for what they need, they have more time to focus on creating value.
Having the right tools, materials, and information readily available eliminates unnecessary searching and movement, reducing wasted time and effort while boosting efficiency.
Schedule
The schedule plays a key role in the 5S process, particularly during the Sort phase. The schedule can be used as a guide to help workers identify the current phase of work, leading to a focused 5S cycle.
Additionally, the pull plan provides workers with insight into upcoming tasks for each phase of work. This allows them to anticipate the materials and tools needed in a specific area, ensuring everything is in place to support efficient completion.
Since 5S is a continuous cycle, it is especially important to repeat the process whenever one phase of work is completed, and a new one begins.
Learn 5S at LCI
The Lean Construction Institute is committed to transforming the design and construction industry by providing educational resources, conducting research, and facilitating local and national Lean events. Explore supplementary resources below to further your understanding of 5S .
Lean Assessments
How strong is your Lean knowledge? Take a Lean assessment to determine your current state so you have a baseline for improvement. Lean assessments are available for individuals, teams, and organizations alike. Whether you’re new to Lean or are an experienced Lean practitioner, Lean assessments are a great way to get started at LCI!
TAKE ASSESSMENTMore Lean Topics
From 5s to IPD, explore popular Lean design and construction topics below.