Kaizen
(Continuous Improvement)
An Introduction to Kaizen
In a Lean system, maintaining a mindset of continuous improvement is necessary for a team to thrive. In fact, “continuous improvement” is one of the six tenets of the Lean Construction Institute that every Lean enterprise should abide by. Kaizen is the manifestation of that mindset.
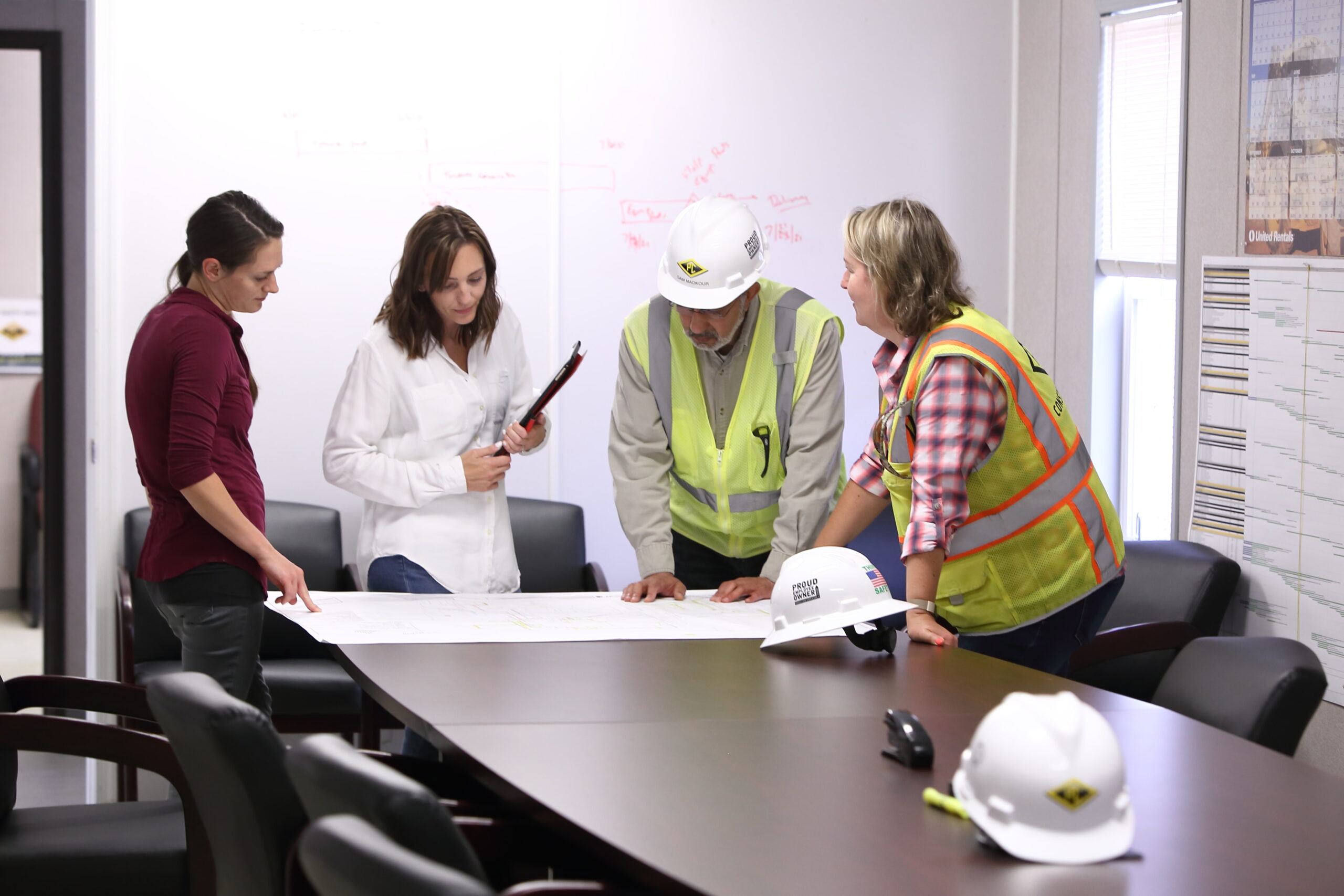
What Does Kaizen Mean?
“Kaizen” is the Japanese word for continuous improvement. Kaizen has come to mean the philosophy of continuous improvement. In Lean thinking, we are always aiming to improve our processes and maintain a mindset of Kaizen.
Kaizen in Lean Design & Construction
In a Lean project, team members at all levels are encouraged to voice their thoughts and provide suggestions for how processes can be improved. Building that environment starts at the management level and requires a team that is built on its members trusting one another.
By maintaining a mindset of continuous improvement, we can foster an environment where innovation can occur. Failing to embrace the Kaizen methodology results in one of the most overlooked of the 8 wastes of Lean – unused creativity of team members.
When seeking areas for improvement, it’s important to focus on the process rather than the people. As American engineer W. Edwards Deming astutely pointed out, “Eighty-five percent of the reasons for failure are deficiencies in the systems and process rather than the employee. The role of management is to change the process rather than badgering individuals to do better.”
Kaizen Mindset
The Kaizen process should be framed as a discussion of process rather than an excuse for workers to air their grievances with someone they have a personal issue with. Such concerns should be addressed with management in a private forum and are not what adopting a Kaizen mindset is about.
Kaizen Thinking
One common concern in the design and construction community is that the three pillars of cost, quality, and safety cannot be improved without sacrificing one. Lean and Kaizen thinking are both in contrast to this philosophy; anything can be achieved through maintaining a mindset of continuous improvement.
What is a Kaizen Event?
A Kaizen event is a workshop-style event in which all members of a project team gather together to discuss major process changes. This event often takes as many as 3-5 days depending on the size and scope of the project in question.
Kaizen events often include other Lean tools such as Value Stream Mapping, A3 Thinking, and 5S as teams work to break down various problems.
A Kaizen event should include all parties that are impacted by the processes being discussed. The goal at the end of one of these events is that the group comes out of it with several ideas for process improvement.
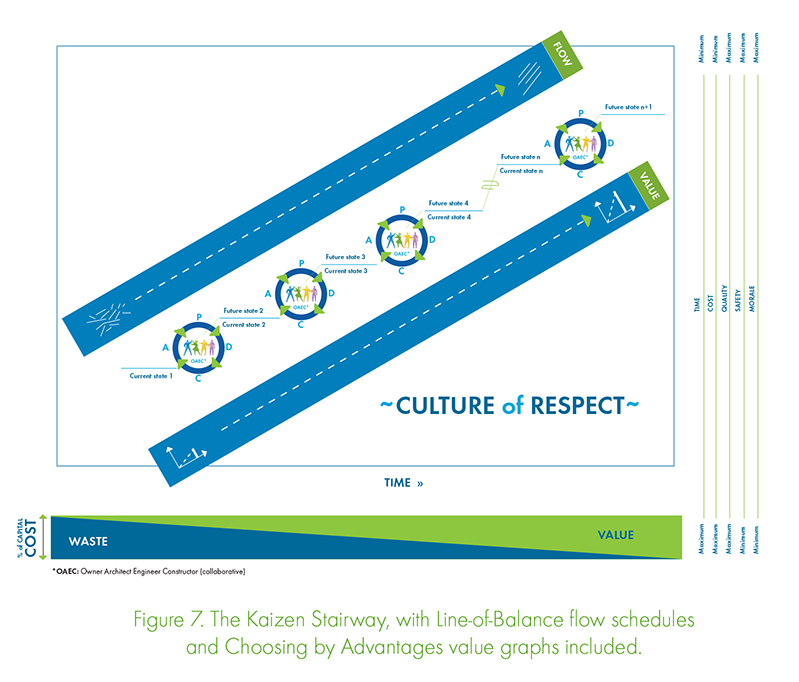
The Language of Kaizen
When having a process improvement discussion, it’s important that the manager leading the discussion maintains an open mind rather than assuming they have all of the answers. Ask questions rather than providing the solutions.
Kaizen Discussions
Some common questions that can drive discussion include:
- “Why are we doing this process this way?”
- “How can we make this more efficient?”
- “Where do we need more help?”
- “Where are stoppages in the workflow where work is waiting on something else?”
- “How can we do it better?”
Improving Workflow & Performance
The discussion of these queries should be a team effort. All team members should feel comfortable providing feedback in an open forum and it is the job of management to not get defensive when process criticisms are levied.
Add these discussions to your regular workflow. Plan scheduled process improvement meetings so that team members don’t feel like the discussions only take place when management is unhappy with team performance.
The more normalized Kaizen discussions are, the more comfortable workers will be voicing their concerns when they arise. Kaizen is an opportunity for growth. No process is perfect and identifying problems in the workflow should be seen as a positive rather than a negative.
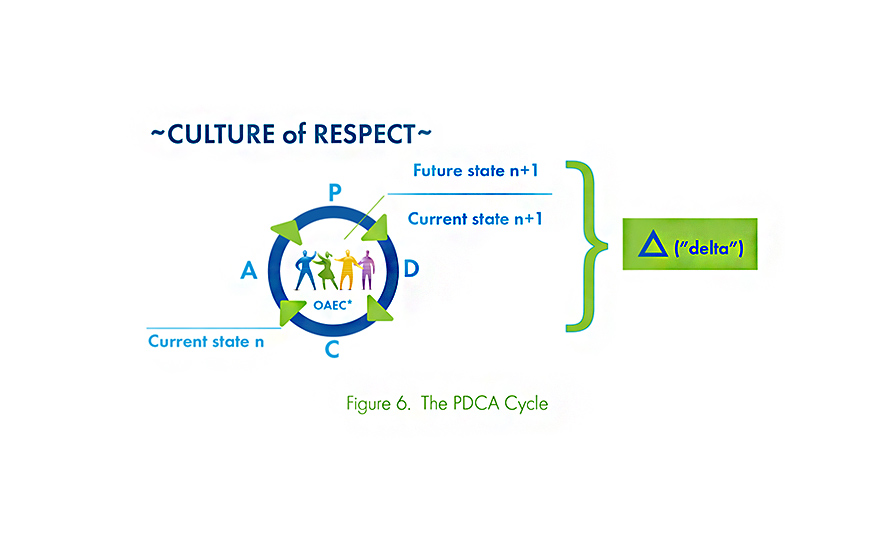
The PDCA Cycle
This may sound counterintuitive, but: the standardization of processes is necessary for creating a system where continuous improvement can thrive. The more standardized processes are across the board, the easier it is for workers to universally implement small or big changes. A system in which everyone does things differently will lead to varied results, making it impossible to analyze the changes tested during an A3 experiment or otherwise. With a standardized system, the PDCA cycle can take over, leading to beneficial long term changes.
Kaizen & PDCA
A Lean Model
PDCA stands for Plan, Do, Check, Adjust and it is one of the most effective Lean models for achieving operational excellence. The cycle is a means of testing potential process changes.
Once one PDCA cycle ends, another begins. The future state of one process is the current state of the next. The mindset of continuous improvement is…well, continuous. The end goal is to create a design and construction process that is more efficient, delivering better outcomes to the stakeholders and eliminating waste along the way.
For Process Improvement
- Plan: Decide to make a change and dictate how the change will be implemented and measured.
- Do: Implement the change in the process over a certain period of time.
- Check: Use the predetermined measurements to analyze how successful the change was in achieving the desired result.
- Adjust: If it worked, make the change a permanent part of the future state. If it did not work, aim to determine what went wrong and what your team can do next time instead.
Learn Kaizen & Continuous Improvement
The Lean Construction Institute is committed to transforming the design and construction industry by providing Lean educational resources, conducting research, and facilitating local and national Lean events. It is only through the power of the LCI Corporate Members that LCI is able to offer the supplementary resources below.
Lean Assessments
How strong is your Lean knowledge? Take a Lean assessment to determine your current state so you have a baseline for improvement. Lean assessments are available for individuals, teams, and organizations alike. Whether you’re new to Lean or are an experienced Lean practitioner, Lean assessments are a great way to get started at LCI!
TAKE ASSESSMENTMore Lean Topics
From 5s to IPD, explore popular Lean design and construction topics below.