Lean in Design
(Lean A&E)
An Introduction to Lean Architecture & Engineering
Lean in the Design phase is crucial for achieving successful project outcomes. By integrating builders and design teams from the outset, Lean design focuses on delivering maximum customer value in the most efficient way possible.
This collaborative approach eliminates waste caused by traditional siloed thinking and lack of coordinated planning, which often leads to rework and diminishes value for the customer. By fostering a culture of continuous improvement and shared understanding, Lean Design ensures that the project is optimized for both constructability and customer satisfaction.
What is Lean in Design?
Lean in design focuses on four key concepts: team collaboration, problem solving, decision making skills and sharing information. With a Lean mindset, design engineers and architecture teams can share information freely and collaboratively to solve difficult problems and make decisions quickly and efficiently. Thus, design professionals increase value for the customers and for the stakeholders.
Thinking Differently with Lean Integrated in Design
Lean design fosters a different approach to design. Lean focuses heavily on driving innovation and design excellence by removing the eight types of waste found in any design process. Through the elimination of waste, bottlenecks are removed resulting in timelier decisions, and better information flow. From an overabundance of information and data to underutilized talent, the 8 wastes are as follows.
- Defects – The production of defective parts, work or information that causes the work to be scrapped or redone
- Over/Under Production – Making something before it is truly needed.
- Waiting – When work-in-progress or people are waiting on the next step in production.
- Not Utilizing Talent – When a team loses time, ideas, skills, improvements and learning opportunities by not engaging or listening to employees.
- Transportation – Includes creating inefficient transport, moving raw materials, parts, equipment, or information into or out of storage or between processes.
- Inventory – Occurs when product, materials, work-in-progress or information quantities go beyond supporting the immediate need.
- Motion – Unnecessary movement by people or movement that does not add value.
- Extra Processing – Taking unnecessary steps in a process.
By understanding and eliminating waste in the design phase of a project, we can achieve significant benefits for everyone involved.
For example, teams can work more efficiently by streamlining communication channels and reducing unnecessary revisions. This leads to better collaboration across the team while working seamlessly together from the earliest stages.
Reduced stress is another major benefit, as a streamlined workflow minimizes confusion and errors, providing workers a more fulfilling work experience with clear responsibilities and efficient processes. This allows them to focus on their core contributions.
Clients benefit from minimized rework, faster delivery times due to efficient coordination and approvals, and ultimately, a higher-value building that better meets their needs and budget. This focus on efficiency and value not only improves the design process itself, but also elevates the quality and impact of the final built environment.
Lean Thinking in the Design Phase
Lean thinking in design focuses on maximizing value by eliminating waste and fostering a collaborative environment. This approach breaks down traditional silos between owners, design teams, and builders, enabling early integration of key stakeholders. This leads to more informed decision-making, proactive planning, and reliable commitments throughout the project lifecycle.
By clearly defining conditions of satisfaction, the entire team remains focused on the end goal, ensuring a successful outcome that meets client needs and project objectives. Ultimately, Lean thinking streamlines the design process, reduces wasted effort, and enhances value for all involved.
Lean thinking in design transcends “business as usual” by actively challenging constraints and promoting a culture of continuous improvement. By fostering collaboration and eliminating waste, Lean practices help design teams achieve remarkable results.
Benefits of Lean Thinking in the Design Phase
1. Reduced Cycle Times
Streamlined communication, smaller batching of design packages, and collaborative decision-making processes accelerate project delivery. This eliminates the traditional “throwing work over the fence” approach, where design packages are completed in isolation and then passed on to the next stage, often leading to delays and rework.
2. Rapid Advancement
Collaborative planning and problem-solving in Big Room settings drive efficient progress.
3. Optimized Resource Allocation
Effective resource management across multiple projects maximizes productivity and minimizes waste.
4. Value-Driven Design
By engaging stakeholders early and establishing target value goals, Lean design avoids the need for costly and time-consuming de-value engineering exercises after the design is complete. This ensures that the design meets both client needs and budget constraints from the outset.
Benefits of Early Stakeholder Involvement in the Design Phase
Engaging all stakeholders – owners, contractors, subcontractors, and the entire design team – unlocks a wealth of perspectives and expertise. This leads to:
1. Enhanced Problem-Solving
Teams can creatively and effectively address challenges, leading to better design solutions.
2. Improved Design Outcomes
The integration of diverse viewpoints results in a higher quality product that truly meets client needs.
3. Increased Value
By optimizing resources, reducing waste, and accelerating schedules, Lean delivers greater value to all stakeholders.
Why Apply Lean in the Design Phase?
In today’s world, design suffers from lack of collaboration, indecisiveness, a high rate of change, lack of resources and siloed processes. The design-build and design-bid-build contract structures inherently prevent collaboration between design and construction phases, which leads to rework, working over budgeted hours (labor resources) and reactivity and firefighting with no problem solving
As a result of this, 70% of construction projects are delivered late and 73% are delivered over-budget. This is due to an excess of rework requests and high amounts of waste, leading to dissatisfied customers and shrinking profit margins. In fact, just 9% of owners believe they are achieving a high level of excellence in total project performance.
Common design constraints are often exacerbated by traditional contracting strategies that purposefully create silos between teams and restrict information flow. This fragmentation hinders collaboration and creates an environment where rework, budget overruns, and reactive “firefighting” become the norm. Instead of fostering proactive problem-solving, these outdated approaches perpetuate a cycle of inefficiency and frustration. This leads to increased labor costs as teams work over budgeted hours to address unforeseen issues and rework designs.
Lean design, on the other hand, challenges these conventional practices by promoting transparency, collaboration, and a unified project approach. By breaking down silos and fostering a shared understanding of project goals, Lean empowers teams to proactively address challenges, optimize resources, and deliver exceptional value.
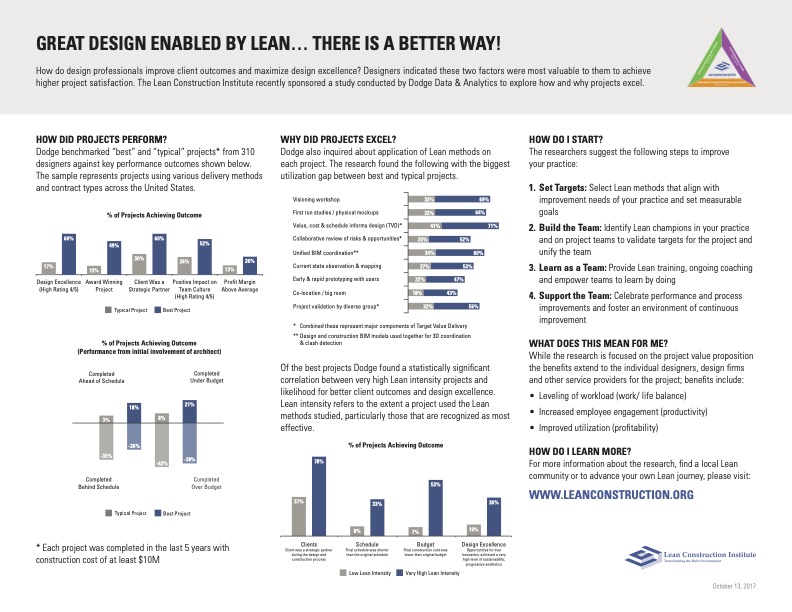
LCI Research
LCI and Dodge Data and Analytics benchmarked “best” and “typical” projects from 310 designers against key performance outcomes shown below. Of the best projects Dodge found a statistically significant correlation between very high Lean intensity projects and likelihood for better client outcomes and design excellence.
Download LCI Research: Great Design Enabled by Lean
Benefits of Lean Architecture & Lean Engineering
Design firms and teams who embrace Lean methods experience a significant boost in productivity, leading to improved project outcomes for the organization and the client. They see increased profitability, a higher percentage of projects delivered on time and within budgeted hours, and a greater ability to meet client needs.
Most importantly, Lean thinking fosters a culture of continuous improvement, resulting in higher levels of design excellence and innovation. By prioritizing value creation and eliminating waste, Lean empowers designers to deliver exceptional results that surpass expectations.
What is Target Value Delivery (TVD) in Lean Design?
Target Value Delivery (TVD) is a disciplined management practice used from the very beginning of the design phase and continued throughout the entire project lifecycle. It ensures that the project meets the operational needs and values of its users while staying within the allocated budget. By establishing the target value at the onset, contractors, owners, and designers can collaborate to achieve innovation throughout the design process, increasing value by saving time, money, and human effort. This collaborative approach minimizes waste often produced by the design-estimate-redesign cycle(s) common in traditional value engineering approaches.
How to Implement a Lean Operating System in the Design Process
If you believe that utilizing a Lean system of project delivery is the right step for your next project, consider familiarizing yourself with Lean principles, practices, and design tools. Lean Project Delivery provides a collaborative framework that enhances the design phase by promoting early stakeholder involvement, optimizing workflow, and ensuring alignment between design, construction, and client goals.
Understand the Lean Principles of Design
The first step towards implementing Lean in the design development process is to adhere to the Six Tenets of the Lean Construction Institute:
Utilizing Lean Design Practices & Tools
Lean designers can take advantage of several practices and tools to streamline their implementation of Lean methods.
Work Cluster Organization
A selection of leaders from coordinating teams that remain in constant coordination and communication with one another to enhance flow and decrease waste.
Big Room Mindset
A project approach aimed at bringing key individuals together to speed up communication, improve decision-making, and reduce siloed thinking or approaches.
Last Planner System® in Design
A system for project production planning and control, aimed at creating a workflow that achieves reliable execution.
A3 Thinking
A collaborative Lean methodology that facilitates PDCA thinking in action—Plan, Do, Check, Act—to encourage proactive problem-solving, continuous improvement, and incorporate all key stakeholder perspectives.
Set-Based Design
A method that keeps requirements and options flexible for as long as possible in the design process, carrying forward viable options in sets. This reduces the waste associated with traditional point-based design by exploring multiple solutions concurrently and delaying convergence on a single solution until the optimal choice is clear.
Conditions of Satisfaction
Conditions of Satisfaction (COS) are a critical tool for establishing a shared understanding of what constitutes success for a project. They go beyond traditional metrics like budget and schedule to define specific, measurable, achievable, relevant, and time-bound (SMART) criteria that ensure the project delivers maximum value to all stakeholders. By clearly outlining expectations and aligning the team on desired outcomes, COS foster accountability and drive performance throughout the project lifecycle.
Learning Lean in Design
The Lean Construction Institute is committed to transforming the design and construction industry by providing educational resources, conducting research, and facilitating local and national Lean events. It is only through the power of the LCI Corporate Members that LCI is able to offer the supplementary resources below to further your Lean journey.
Lean Assessments
How strong is your Lean knowledge? Take a Lean assessment to determine your current state so you have a baseline for improvement. Lean assessments are available for individuals, teams, and organizations alike. Whether you’re new to Lean or are an experienced Lean practitioner, Lean assessments are a great way to get started at LCI!
TAKE ASSESSMENTMore Lean Topics
From 5s to IPD, explore popular Lean design and construction topics below.